Flat Flexible Cables (FFC): A Cost-Effective and Scalable Interconnect Solution
Sara Hu2025-07-24T15:13:32+00:00For engineers balancing performance, flexibility, and cost, Flat Flexible Cables (FFC) remain one of the most efficient interconnect solutions in electronics today. Their simple structure, adaptability, and low manufacturing cost make them ideal for countless applications—from consumer electronics to industrial controls, smart home, industrial equipment, vehicles, electric cars, medical safety and appliances.
And while they may appear simple, there’s a surprising range of design options and technical capabilities behind a well-optimized FFC solution.
What Are FFCs?
Flat Flexible Cables consist of flat copper conductors laminated between thin layers of polyester (PET) or polyimide (PI) insulation. They’re designed to be in one direction, making them ideal for compact, folding, or sliding assemblies.
Available in pitches from 0.5 mm to 2.54 mm and lengths up to 10 meters, FFCs can be designed with custom conductor widths, pitches, surface finishes, EMI shielding, stiffener, impedance and high-frequency transmission configurations—all while remaining mass-producible at low cost.
Where FFCs Make Sense
Low-Cost Internal Interconnects
Used widely in consumer electronics, displays, small appliances and communication devices, FFCs are ideal when low voltage and short-run connections are needed without overengineering the solution.
Space-Constrained or Hinged Designs
FFCs maintain a low Z-height and tight bend radius, making them perfect for hinged, folding, or sliding assemblies—especially in automotive interiors, control panels, or embedded screens.
Simplified Assembly
With support for ZIF/LIF connectors, IDC, hot bar soldering, or crimped terminals, FFCs help reduce assembly time and connector cost across production lines.
Why FFCs Are Cost-Effective
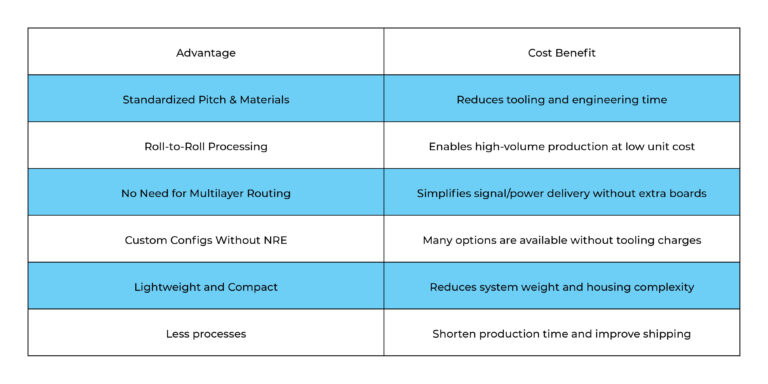
Engineers can replace point-to-point wiring, reduce BOM size, and eliminate unnecessary PCB layers—all using an off-the-shelf or semi-custom FFC design.
Key Design Options Engineers Should Know
Materials
• Dielectrics: PET (standard, UL PET or Non-UL PET optional), PI (high-temp or flex), optional shielding (1 or 2 sides)
• Adhesives: Epoxy, acrylic
• Conductor: Copper, with thicknesses from 0.035 mm to 0.3 mm or any customized thickness W/T Ratio≤20
• Finishes: Bare, Tin, or Gold plating
Connector Support
• ZIF / LIF (standard for low-insertion-force assemblies)
• IDC (insulation displacement)
• Crimp, hot bar soldering, or direct board-mount
• Custom connector-to-cable assembly available
Need a compact, flexible interconnect for your next design?
Explore our custom FFC solutions and get expert guidance from our engineering team today.”
Mechanical Enhancements
• Pre-folded or pre-bent configurations
• Punching, slanting, and stiffeners (PI or PET)
• EMI shielding for signal integrity in sensitive systems
FFC vs. Other Interconnect Options
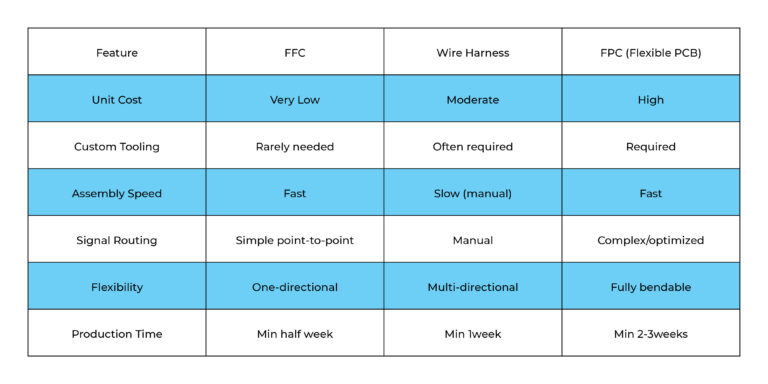
Final Thoughts
Flat Flexible Cables offer a low-profile, low-cost, and easily manufacturable solution for simple interconnect needs. Whether used in volume production or early-stage prototyping, FFCs are one of the most efficient options available to engineers seeking to simplify wiring and reduce cost—without compromising reliability.
At PICA Manufacturing Solutions, we support a wide range of FFC designs with custom lengths, Surface Finish, terminations, shielding, and assembly options to match your system needs.