Precision Cleaning with PICA: Ultrasonic PCB Cleaning at Our Kuala Lumpur Facility
Michael Bedard2025-07-24T14:40:01+00:00At PICA, we know that the performance and reliability of printed circuit boards (PCBs) depend heavily on their cleanliness. That’s why our Kuala Lumpur facility is equipped with advanced ultrasonic cleaning technology, ensuring every PCB meets the highest quality standards.
What Is Ultrasonic Cleaning?
Ultrasonic cleaning uses high-frequency sound waves, typically between 20 and 40 kHz, to create microscopic bubbles in a cleaning solution. This process, known as cavitation, generates tiny shockwaves that dislodge contaminants from every surface of the PCB—even in hard-to-reach areas under components and inside vias.
Unlike manual or spray cleaning methods, ultrasonic cleaning reaches areas that traditional approaches cannot, ensuring a superior level of cleanliness that translates into better performance and reliability for your electronics.
Benefits of Ultrasonic Cleaning for PCBs
- Thorough Cleaning
Ultrasonic waves penetrate even the smallest crevices, effectively removing flux residues, solder paste, and other contaminants from densely populated boards.
- Gentle Yet Powerful
Despite its intensity, ultrasonic cleaning is gentle on delicate PCB components when performed correctly. The process uses mild cleaning agents and controlled frequencies to avoid any damage.
- Time Efficiency
Manual cleaning is time-consuming, especially for complex assemblies. Ultrasonic cleaning significantly reduces the cleaning cycle, allowing manufacturers to improve throughput without compromising quality.
- Improved Reliability
Cleaner PCBs result in fewer defects, longer product lifespans, and reduced chances of field failures—crucial benefits for industries like aerospace, medical devices, and automotive electronics.
- Consistent Cleaning
Ultrasonic cleaning ensures uniform cleanliness across all areas of the PCB, even the most intricate parts. Manual methods often struggle to achieve this level of consistency.
- Eco-Friendly Solution
Ultrasonic cleaning typically requires less aggressive chemicals than traditional methods, reducing environmental impact while maintaining superior results.
Expert Insights on PCB Manufacturing Processes
Stay ahead with the latest best practices, innovations, and strategies to enhance efficiency, quality, and reliability in PCB manufacturing. Explore in-depth industry expertise—read our manufacturing blog today!
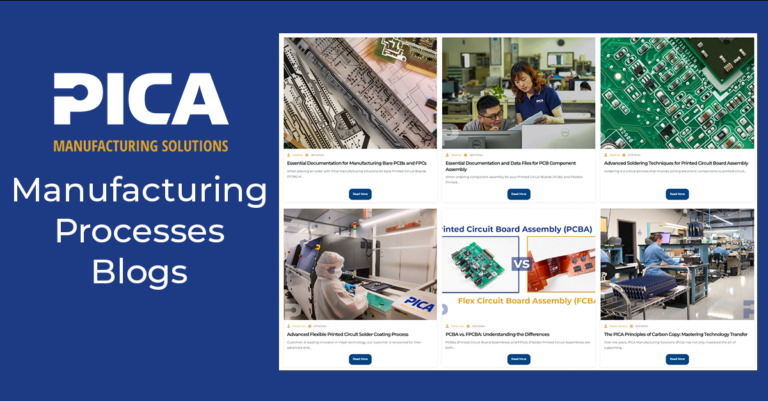
Key Considerations for Ultrasonic Cleaning
While ultrasonic cleaning offers clear advantages, following best practices is essential to achieve optimal results and prevent damage to sensitive PCBs:
- Frequency Matters
- Lower frequencies (20–25 kHz) generate more powerful cavitation but can be harsh on sensitive components.
- Higher frequencies (35–40 kHz) provide gentler cleaning, making them ideal for PCBs.
- Cleaning Time Matters
- The duration of exposure to ultrasonic cleaning impacts how thoroughly a PCB is cleaned. At PICA, we control this process meticulously.
- Proper Cleaning Solution
- We use PCB-safe cleaning agents designed to protect solder joints, conformal coatings, and sensitive materials.
- DI Water Pollution Level Monitoring
- We use a conductivity meter to ensure that the deionized (DI) water used for rinsing is ultrapure and free of ionic contamination.
- Rinsing and Drying
- Thorough rinsing with deionized water and proper drying are essential to prevent residue buildup and moisture retention.
- Avoid Overexposure
- Excessive exposure can cause damage. At PICA, we carefully control cleaning times to preserve board integrity.
Discover the PICA Difference
Ultrasonic cleaning is just one way we invest in advanced technology to deliver the highest quality PCBs at our Kuala Lumpur facility. From precise cleaning to rigorous inspection, we ensure every board meets your exacting standards.
Contact PICA today to learn more about how our ultrasonic cleaning services can enhance the quality and reliability of your PCBs. We’re here to help you succeed.