Kapton Etching in Flex Circuit Manufacturing: Processes, Materials, and Considerations
Simon Lim2025-07-23T17:47:24+00:00In the world of flexible electronics, polyimide films like Kapton® (a DuPont trademark) are a foundational material. Used in everything from flex circuits and medical sensors to MEMS and microfluidic systems, Kapton’s thermal stability and dielectric properties make it ideal—but in many applications, selective removal or patterning of the film is required. This is where Kapton etching comes in. While mechanically removing polyimide is possible in some cases, wet chemical etching remains the most common method for achieving precise, repeatable results in production environments.
What Is Kapton Etching?
Kapton etching is the selective removal of polyimide film using chemicals that dissolve the material only in unprotected areas. It’s used to:
• Create openings or channels in flex circuits
• Define microfluidic features
• Expose layers in MEMS or sensor assemblies
• Pattern areas for selective bonding, coating, or metallization
The process typically uses strong alkaline solutions and a resist mask to define which areas of the Kapton remain.
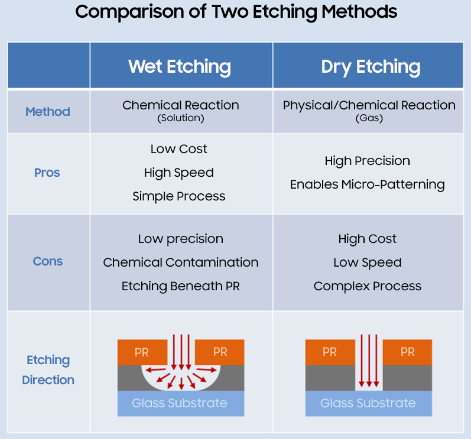
Source: Global Samsung Display
Wet Chemical Etching: Key Concepts
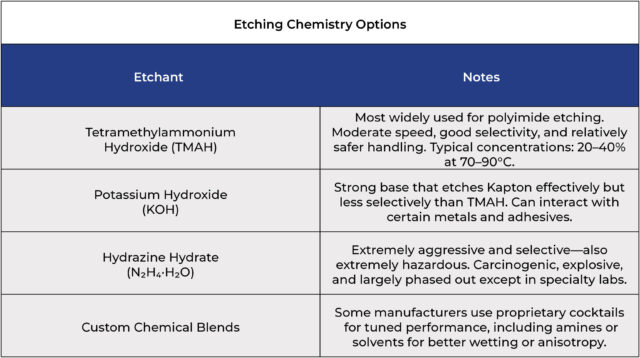
Etching Process Overview
1. Cleaning
• Remove oils and contaminants with solvents (IPA, acetone) or plasma.
• Clean surfaces ensure proper adhesion of the masking layer.
2. Masking
Apply a chemical-resistant mask to protect areas that should remain:
• Photoresist: Applied via spin coating, then exposed and developed—best for fine patterns.
• Metal Masking: Deposited chrome, gold, or aluminum patterned using lithography or lift-off. Excellent chemical durability.
• Adhesive Films or Stencils: Lower-cost alternative for coarse features.
3. Etching
Immerse or spray the masked Kapton in a heated alkaline bath(TMAH, KOH, etc.). Etch rate depends on:
• Solution concentration
• Temperature
• Time
• Mask design and feature size
4. Rinse & Quench
Immediately rinse with DI water to halt etching and remove chemical residues.
Ready to Bring Your Designs to Life with Flex?
Partner with PICA for flexible circuit boards engineered for performance, precision, and durability. Let’s build smarter, smaller, and more reliable electronics—together.
5. Mask Removal
Strip off the photoresist or dissolve the metal mask using appropriate solvents or etchants.
6. Final Cleaning & Drying
Clean the surface to remove any remaining by products, then dry for downstream processing.
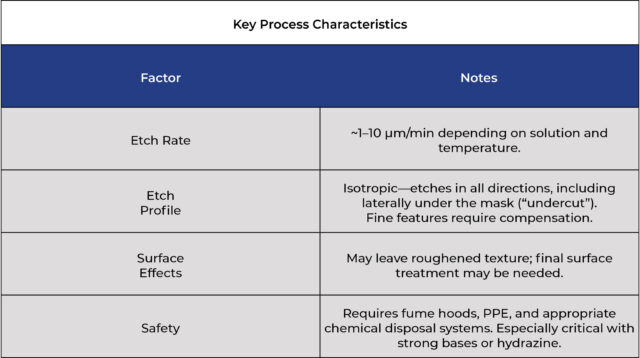
Design Considerations for Engineers
If your flex circuit requires Kapton openings or channel features, it’s important to:
• Account for undercut in your design rules—especially for tight geometries
• Choose a mask type appropriate for your chemical and resolution needs
• Confirm adhesive or copper layer compatibility with etchants like KOH
• Coordinate with your manufacturing partner early to ensure optimal feature definition

Final Thoughts
Whether you’re developing advanced flex sensors, disposable medical test devices, or multilayer flexible circuits, understanding the Kapton etching process is essential for success. The choice of chemistry, masking strategy, and design rules all contribute to achieving the precision and reliability required in production.
At PICA Manufacturing Solutions, we support customers through the full flex circuit lifecycle—from design for manufacturability (DFM) to precision etching and final assembly.
If you’re planning to incorporate Kapton patterning or want to explore the possibilities of multi-layer or structured polyimide flex designs, we’re here to help.