Fineline PCB / High Density Interconnect (HDI) PCB
As technology continues to advance at a rapid pace, the demand for smaller, faster, and more powerful electronic devices has reached an all-time high. This is where Fineline PCB / High Density Interconnect (HDI) PCB Electronics Manufacturing comes into play, revolutionizing the world of electronics. These cutting-edge circuit boards are becoming the go-to solution for designers and engineers, offering a higher density of components and interconnections than traditional PCBs.
One of the key advantages of Fineline PCB / High Density Interconnect PCBs is their ability to accommodate a greater number of components in a smaller space. By utilizing intricate layers of copper traces and vias, these advanced circuit boards enable the transmission of signals and power between different components with utmost efficiency. This breakthrough technology allows for a more compact and efficient design, resulting in electronic devices that are not only smaller and more lightweight but also deliver superior performance.
The production process of these intricate circuit boards involves several steps that require precision and expertise. It all begins with Laser Direct Imaging (LDI) that can achieve line and space down to 2mils in mass production and 1 mil in small volume. The next step involves laser drilling, which creates tiny holes for interconnections, allowing for a higher density of components. Then, a series of electroplating processes is employed to form the conductive pathways, followed by the application of multiple layers of insulating material. Finally, the PCB is subjected to rigorous Automatic Optical Inspection (AOI) and flying probe testing to ensure its reliability and functionality.
In conclusion, the production of Fineline PCB / High-Density Interconnect (HDI) PCBs is a complex and intricate process that demands the expertise of skilled engineers and technicians. From designing the layout to laser drilling, electroplating, and layering, each step is executed with precision to create high-quality Fineline PCB / High Density Interconnect PCBs.
These compact and powerful circuit boards are at the forefront of innovation in the electronics industry, enabling the development of smaller, more efficient, and more advanced electronic devices that shape our modern world.
For technical information on PICA’s Fineline Flex PCB capabilities, click the button below.
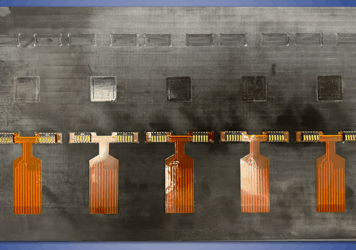
Step-by-Step Guide to the Flex Printed Circuit Board Assembly (FPCBA) Process
IntroductionAs electronics evolve to become thinner, lighter, and more complex, Flex Printed Circuit Boards (FPCBs) have emerged...
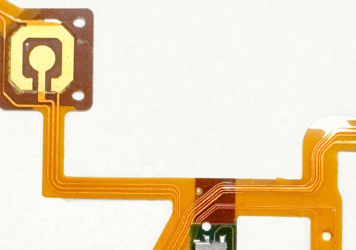
Designing for Precision: Controlled Impedance in Flexible Circuits
As electronic devices shrink and signal speeds increase, one design requirement becomes mission-critical: controlled impedance. This is...
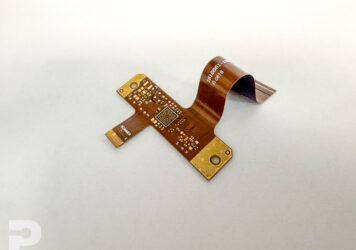
Bending Without Breaking: How Flexible Circuits Are Tested for Reliability
Flexible circuits are built to bend—but only when designed and tested to handle real-world mechanical demands. Whether...

Embedding Performance: How Passive Components Are Integrated into Flexible Circuits
As electronic devices evolve to become smaller, smarter, and more power-efficient, engineers are under increasing pressure to maximize performance within...
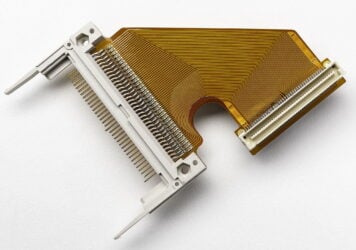
Designing for HDI PCB and Fine-Line Etching: What You Need to Know
As devices shrink and performance demands grow, engineers are turning to High-Density Interconnect (HDI) technology to pack...
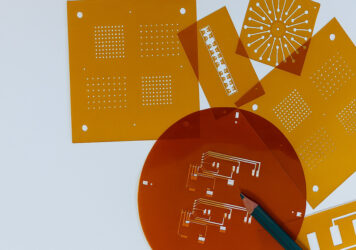
Kapton Etching in Flex Circuit Manufacturing: Processes, Materials, and Considerations
In the world of flexible electronics, polyimide films like Kapton® (a DuPont trademark) are a foundational material. Used in everything...
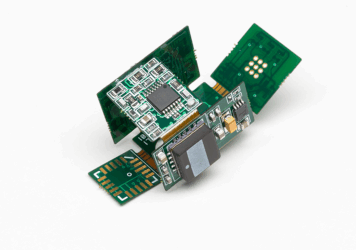
Designing Rigid-Flex Circuits: What Engineers Need to Know
Rigid-flex PCBs combine the best of both worlds—the durability of rigid boards and the versatility of flexible circuits—into a...
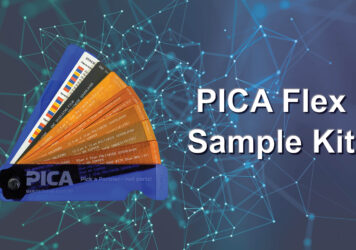
Explore the Possibilities of Flexible Circuit Design with the PICA Flex Sample Kit
Designing flexible circuits isn’t just about choosing the right materials, it’s about understanding how all the pieces come together under...