By strategically investing in X-ray inspection technology, PICA has not only opened doors of opportunity for itself but also for a lot of its customers.
With our state-of-the-art 2D and 3D x-ray equipment, PICA offers real-time inspections for PCB components, assemblies, and other electronic devices. Our team of trained and certified process engineers ensures that every inspection is conducted with precision and attention to detail. Along with on-site inspections conducted at our facility, we also offer remote inspections through our real-time conferencing system. This allows our clients to actively participate in the inspection process, ask questions, and gain a better understanding of the results.
One of the key advantages of X-ray inspections is their ability to identify common defects that can significantly impact product performance.
For example, BGA voiding, where air bubbles are trapped between the ball and the pad, can lead to unreliable connections and compromised functionality. By identifying this defect early in the manufacturing timeline, PICA can take corrective measures, saving precious time, resources, and costs.
Similarly, solder ball wicking, where solder is drawn into the gap between the pad and the component, and misalignment of BGA packages can also be detected through X-ray inspections. These defects can cause short circuits or weak connections, leading to device failure. By catching these issues before they become major problems, manufacturers can ensure the overall quality and reliability of their electronic devices.
But X-ray inspections don’t stop there. They also help identify other critical defects such as solder shorts, joint voiding, and cracks in tracks, joints, and components. These defects can compromise the structural integrity of the device and affect its performance. By detecting these issues early on, manufacturers can rectify them and avoid costly recalls or customer dissatisfaction.
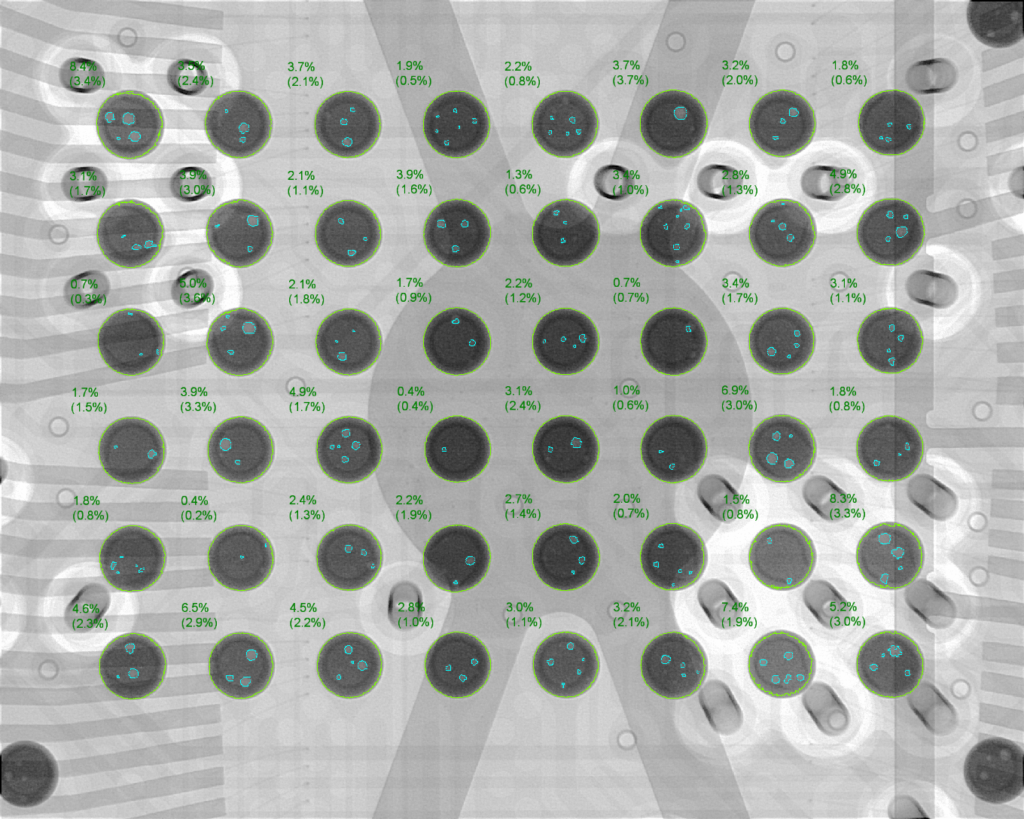
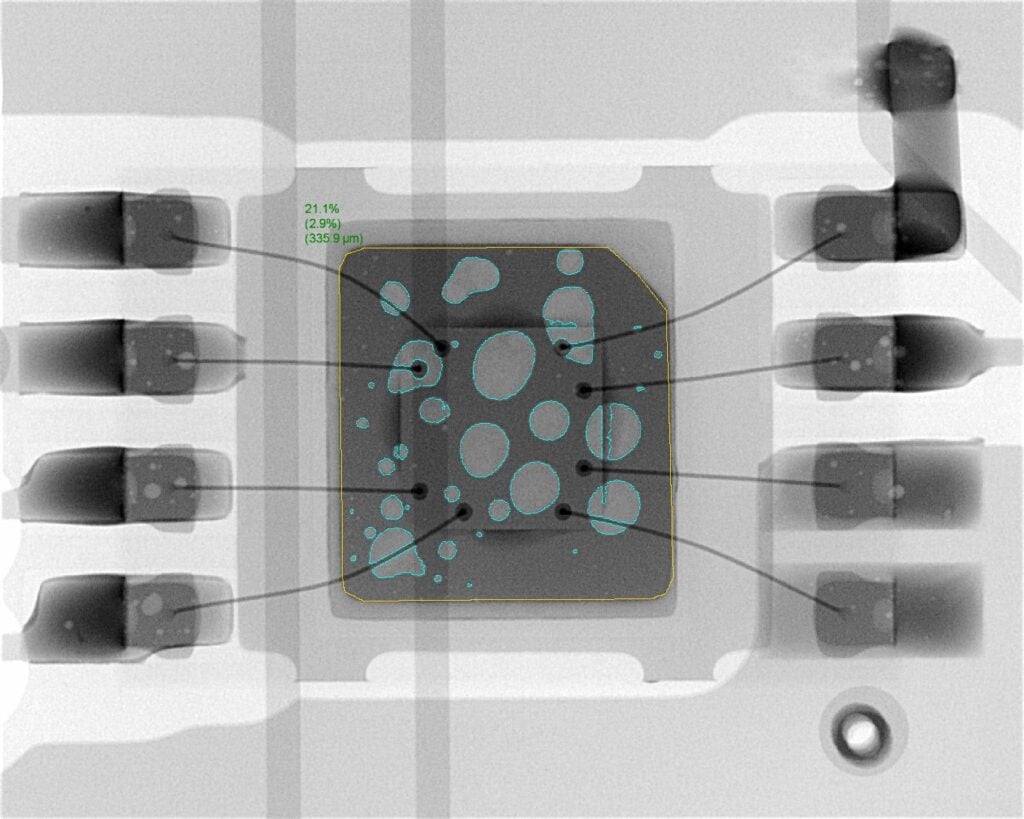
Void Percentage Analysis is a crucial aspect of inspecting printed circuit boards and electronic components. With the help of our advanced x-ray inspection system, we can generate 2D x-ray slices in any plane, allowing us to provide real-time visual analyses of the void percentage. This means that we can quickly and accurately determine the percentage of empty spaces within the components, ensuring the quality and reliability of the product.
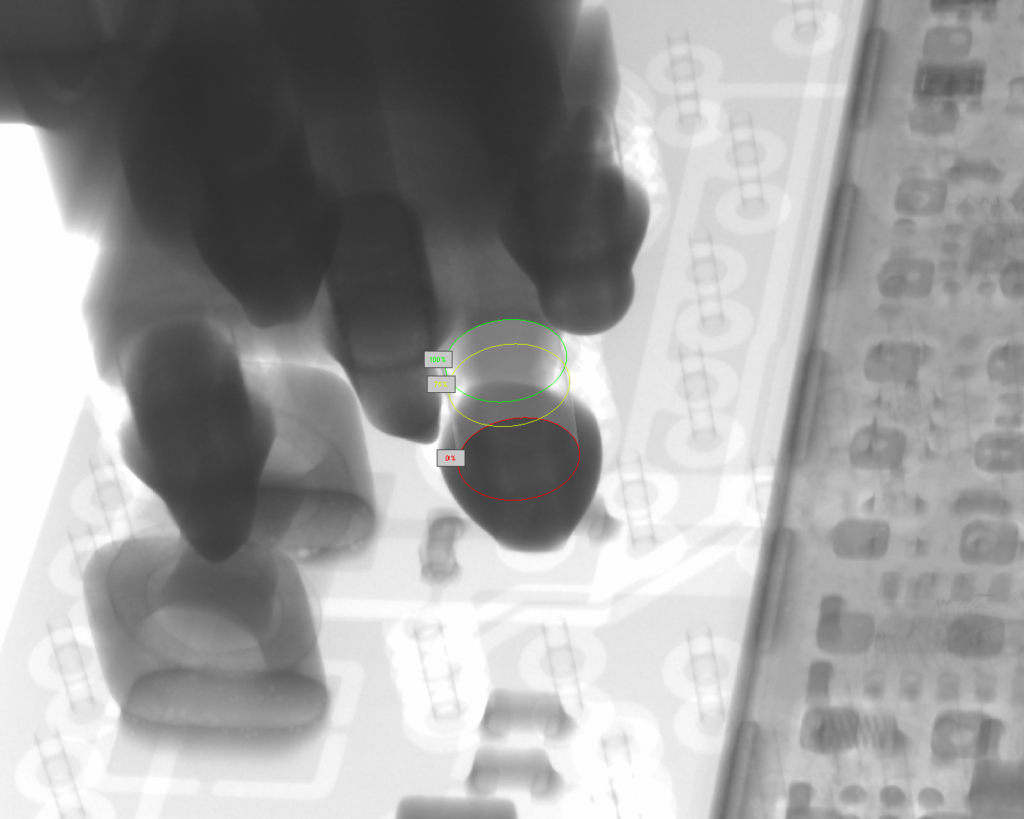
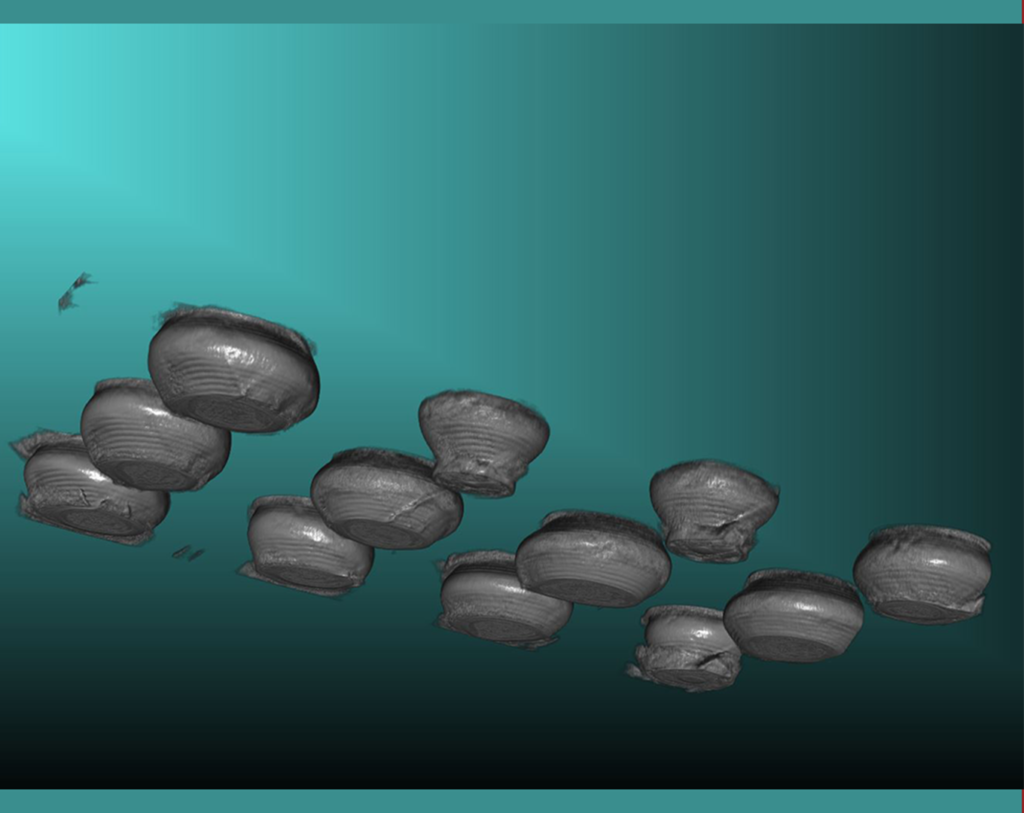
Additionally, our x-ray inspection system also enables us to perform Through-Hole Fill Analysis, giving us seamless visual imaging analyses of the fillings in printed circuit boards and other electronic components.
By utilizing our X-Plane technology, we can produce high-resolution 3D imaging from the 2D x-ray image slices, providing a comprehensive understanding of the component’s structure. Whether it’s analyzing void percentage or assessing the quality of through-hole fills, our x-ray inspection system is an invaluable tool in ensuring the integrity of electronic components.
At Pica, we understand the importance of quality control in the electronics industry. That’s why we offer top-quality X-ray services for PCB inspection. Our state-of-the-art X-ray equipment and highly trained technicians allow us to provide thorough and accurate inspections that meet the demanding standards of your industry.
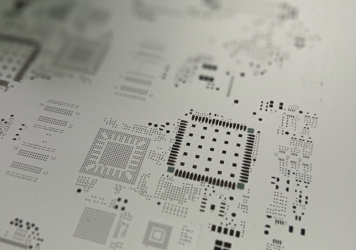
Printed Circuit Board (PCB) Stencil Design: Key Characteristics & Best Practices
Stencil design plays a critical role in ensuring the quality and reliability of printed circuit boards (PCBs). A well-designed stencil...
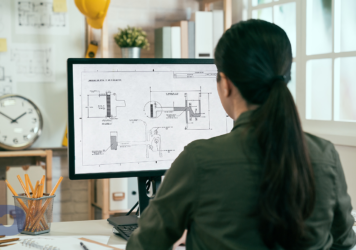
Streamlining PCB Production with DFM at PICA Manufacturing Solutions
Design for Manufacturability (DFM) is a proactive process integral to the PICA Way, ensuring a product design aligns with each...
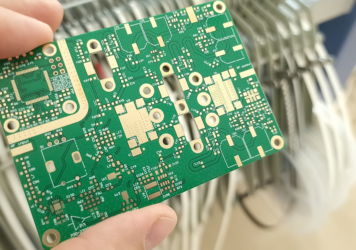
Guidelines for Consigning Components & PCBs to PICA
At PICA Manufacturing Solutions, we occasionally receive printed circuit boards (PCBs) and/or components consigned by our customers for their projects....
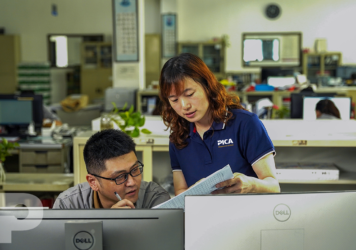
Essential Documentation and Data Files for PCB Component Assembly
When ordering component assembly for your Printed Circuit Boards (PCBs) and Flexible Printed Circuits (FPCs), it's important to...
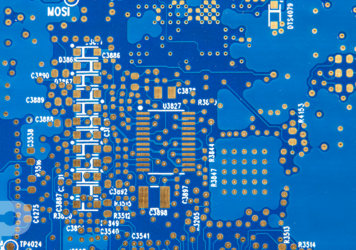
Printed Circuit Board (PCB) Via Protection: Strategies and Standards
This blog is an introduction to a larger white paper that features 7 different via protection types. Download the full white...
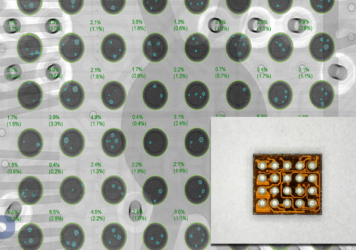
4 factors that can cause voiding in Ball Grid Arrays (BGA)
Ball Grid Arrays (BGAs) are crucial components widely employed in the electronic manufacturing industry owing to their compact size. However,...
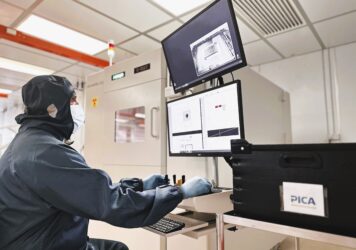
Why X-Ray inspection is essential in flexible printed circuit assembly (FPCA) and printed circuit board assembly (PCBA) processes
In the realm of flexible printed circuit assembly (FPCA) and printed circuit board assembly (PCBA), X-ray inspection...
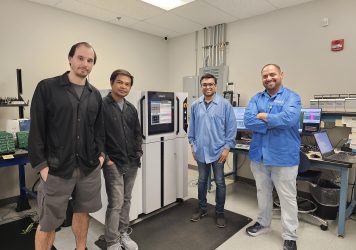
OMRON AOI
We are thrilled to announce that our team at PICA has successfully completed a 5-day training program on the OMRON...