Understanding Tooling in Flexible Printed Circuit Manufacturing: Mechanical Tooling (Part 1)
Pascal Delloue2025-07-24T15:23:34+00:00At PICA Manufacturing Solutions, producing high-quality Flexible Printed Circuits (FPCs) involves a variety of specialized tooling and processes. This blog post, split into two parts, focuses first on the essential mechanical tooling required for FPC manufacturing. Understanding these tools and their functions is crucial for achieving the precision, efficiency, and scalability needed in modern FPC production.
Mechanical Tooling: Soft vs. Hard Tooling
In FPC manufacturing, mechanical tooling is essential for creating precise cuts, slots, and outlines. There are two main types of mechanical tooling: soft tooling and hard tooling. Each serves different purposes depending on the volume, precision, and cost-effectiveness required.
Soft Tooling
Soft tooling refers to cutting dies that are faster and less expensive to produce. These dies are typically made from lower-grade materials and are ideal for small-volume runs or prototypes where precision tolerances are not as critical. However, soft tooling has a shorter lifespan, is less accurate, and is not suitable for large-scale production due to its limited durability.
Two common forms of soft tooling are Steel Rule Dies (SRD) and Etched Dies:
- Steel Rule Dies (SRD): Created by bending a steel blade into the desired shape and mounting it into a die board, SRDs are widely used for cutting flexible materials such as FPC substrates. They are especially suited for low- to medium-volume production because of their quick and cost-effective setup.
- Etched Dies: Etched dies are manufactured by chemically etching a metal plate to create a cutting edge. These dies are typically used for lower-volume runs and applications where extreme precision is not required. Etched dies offer a cost-effective and relatively fast option for creating detailed but less durable cutting tools. They are especially beneficial for prototyping and small runs due to their quick turnaround time.
Key Characteristics:
- Lower cost and faster to produce
- Less precise and shorter lifespan
- Not efficient for large-scale production
- Includes Steel Rule Dies (SRD) and Etched Dies, both suitable for low- to medium-volume runs
Common Uses:
- Initial cuts for prototype designs
- Small batch productions
- Steel Rule Dies (SRD): Quick and cost-effective cutting of flexible materials
- Etched Dies: Fast and affordable cutting for low-precision or prototype applications
- Applications where tight tolerances are not critical
Need Flex PCB Information?
Visit our Flexible Printed Circuit Boards product page to learn more about our capabilities and explore additional informative blogs on flex PCBs.
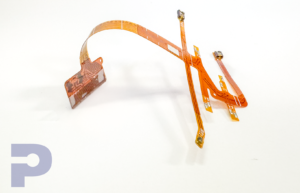
Hard Tooling
Hard tooling, on the other hand, involves precision dies that are designed for long-term, high-volume production. These tools are made from high-grade materials, allowing them to hold tighter tolerances and produce highly accurate cuts. While hard tooling is more expensive upfront—often 10 times the cost of soft tooling—it is much more cost-efficient for larger production runs due to its longevity and ability to be refurbished.
Key Characteristics:
- Highly precise with tight tolerances
- Long lifespan and can be refurbished
- More efficient for large-scale production
- Higher initial cost but better long-term value
Common Uses:
- High-precision cutting for large-scale FPC production
- Long-term production runs requiring consistent accuracy
- Applications where high tolerances are essential
Utilization of Mechanical Tools in FPC Manufacturing
Mechanical tooling plays a crucial role at various stages of FPC production, particularly in preparing materials and shaping the final product. Here are some specific applications:
- Separation: Cutting individual circuits from a larger panel.
- Subpanelization: Preparing panels for assembly and testing by creating smaller sections.
- Partial cuts and slots: Making precise cuts or openings within the FPC design.
- Final outline cutting: Ensuring the final product meets specific dimensional requirements.
- Stiffener Cutting: Mechanical tools cut the outlines and make inside cuts for stiffeners, which are local rigidizers like Polyimide, Polyester, or FR4 applied to specific areas to add rigidity.
- Coverlay Cutting: Similarly, mechanical tools are utilized to cut coverlay, the top layer dielectric that protects the entire circuit surface.
- EMI Shields: Cutting electromagnetic interference shields for FPCs.
Stay tuned for Part 2 of this series, where we will explore fixtures, artwork films, CNC machining, vision punching, screen printing, and comprehensive testing methods, ensuring every project at PICA Manufacturing Solutions meets the highest standards of quality, precision, and efficiency.
Please contact us with any questions.