Understanding Solder Masks: Types, Processes, and Usage Guidelines
Vivian Zhu2025-07-24T15:58:30+00:00In PCB manufacturing, solder mask isn’t just about making a board look green—it’s a functional layer that protects copper traces, prevents solder bridging, and improves overall assembly yield. But not all solder masks are created equal.
From rigid PCBs to flexible circuits and high-density designs, the type of solder mask used—and how it’s applied—can impact everything from durability to manufacturability. This guide covers the most common solder mask types, their processing methods, and how to choose the right one for your design.
What Is a Solder Mask?
Solder mask is a thin protective layer—usually green, but also available in black, white, red, blue, orange, and more—that covers the non-pad areas of a PCB. It prevents unintended solder from flowing onto traces during reflow and protects the copper from oxidation, moisture, and contaminants.
It’s applied after imaging and etching, but before surface finish and component assembly.
Common Types of Solder Mask
There are several solder mask formulations and application methods, each with trade-offs in performance, process complexity, and cost.
1. Liquid Photoimageable (LPI) Solder Mask
Most common in modern PCB manufacturing.
• Process: LPI is screen- or spray-applied as a liquid, then imaged using UV light through a photomask. The exposed areas are hardened and the rest is developed away, leaving openings for pads.
• Finish: Smooth, thin, and consistent coverage. Great for fine-pitch components.
• Best for: Most rigid PCBs, HDI boards, and any design requiring tight tolerances.
Pros:
• Excellent resolution
• Compatible with high-volume production
• Can be applied to both rigid and flex PCBs (with formulation changes)
Considerations:
• Requires controlled UV imaging and cleanroom conditions
• Not ideal for very thick copper or extremely uneven surfaces
2. Epoxy Screen-Printed Solder Mask
Older, lower-cost method, used less frequently today.
• Process: Thermally cured epoxy ink is pushed through a stencil onto the PCB.
• Finish: Thicker, more textured, lower resolution.
• Best for: Simple, low-density PCBs or non-critical consumer applications.
Pros:
• Low cost
• Simple process, no photoimaging required
Considerations:
• Poor registration accuracy
• Not suitable for fine-pitch components
• Slower to apply in large volumes
3. Dry Film Solder Mask
Used in specialty applications, especially when consistent thickness is critical.
• Process: A dry film (like a solder mask “sticker”) is laminated onto the PCB, exposed with UV, and developed.
• Finish: Uniform thickness, excellent edge definition.
• Best for: High-reliability applications, high-voltage designs, or very fine-line spacing where precise clearance is required.
Pros:
• Clean application with good definition
• Excellent dielectric strength
Considerations:
• Higher material cost
• Less flexible than LPI or epoxy masks
• Can be labor-intensive
Explore smarter manufacturing strategies.
Dive into our latest insights on PCB assembly, flexible circuits, and turnkey solutions—crafted to streamline your production from concept to completion.
4. Flexible Solder Mask
Formulated for flexible PCBs and dynamic applications.
• Process: Usually a variant of LPI, specially formulated for use on polyimide or PET substrates.
• Finish: Highly flexible, can withstand repeated bending without cracking.
• Best for: Dynamic flex circuits, wearable tech, or any design where the board bends in use.
Pros:
• Resists cracking or delaminating during flexing
• Compatible with SMT processes
Considerations:
• Requires precise application and curing
• Can be more expensive than standard LPI
Choosing the Right Solder Mask
Engineers should select a solder mask type based on:
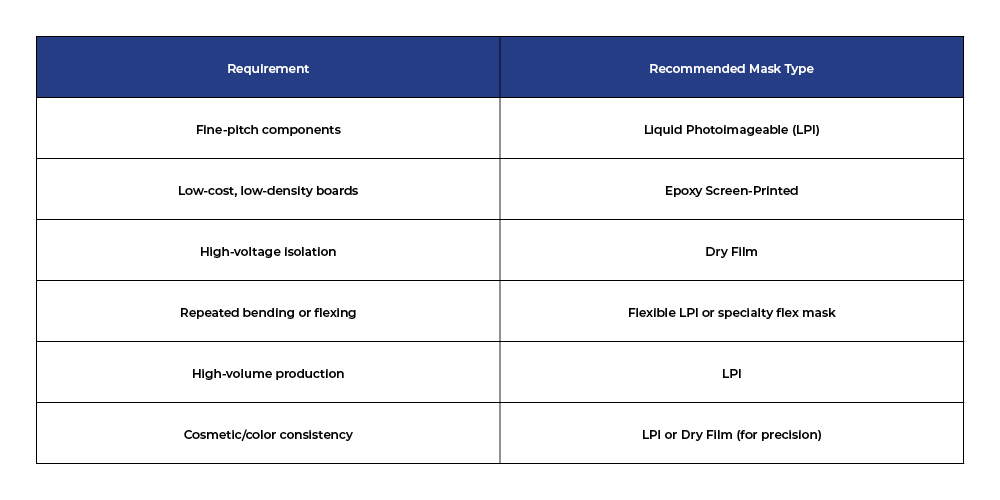
Considerations Beyond the Mask Type
• Color Choice: Green is standard due to high contrast and process stability, but black, white, red, and blue are available—especially for cosmetic or branding purposes.
• Thickness: Thicker masks offer more protection but can interfere with component coplanarity.
• Surface Finish Compatibility: Some masks work better with certain finishes (e.g., ENIG, HASL, OSP).
Final Thoughts
Solder mask may seem like a background player in PCB design, but the type you choose has a direct effect on reliability, manufacturability, and yield—especially in high-density or high-performance designs.
At PICA Manufacturing Solutions, we work closely with engineers to select the right solder mask formulation and process for each application—whether you’re building multilayer HDI boards, low-cost consumer products, or flexible electronics.