Wire Harnesses
PICA Manufacturing Solutions delivers precision-engineered wire harnesses designed to simplify complex electronic interconnections and ensure dependable performance. Our wire harness manufacturing capabilities cover everything from simple point-to-point assemblies to intricate multi-branch harnesses, integrating a variety of wire gauges, connector types, protective sleeving, and strain relief solutions. By consolidating multiple wires into a single organized harness, we help you reduce assembly time, minimize errors, and streamline your production workflow.
Our wire harness solutions are built with quality, consistency, and flexibility in mind. From prototype builds to high-volume production, PICA leverages automated cutting, stripping, crimping, and testing to deliver reliable, repeatable results for even the most demanding applications. Whether you need shielded, molded, or custom-labeled harnesses, our experienced team can support unique configurations while meeting rigorous electrical and mechanical requirements. Trust PICA to deliver wire harness assemblies that keep your systems connected and performing reliably.
Benefits
Simplified Installation: They are pre-assembled which simplifies the installation process saving time during equipment assembly and manufacturing.
Improved Reliability: By eliminating loose wires and connections, wire harnesses reduce the risk of electrical shocks, open circuits and other issues leading to improved overall system reliability.
Space and Weight Savings: Bundling wires together helps optimize space utilization, reduces clutter, and minimizes the overall weight of the system or vehicle.
Enhanced Protection: Wire harnesses are often encased in protective sheaths or tubing providing protection against environmental factors like abrasion, moisture, and chemicals.
Standardization and Quality: The use of wire harnesses allows for standardized manufacturing processes, leading to consistent quality and performance of electrical systems.
Improved Signal Integrity: Proper bundling and shielding of wires within a harness minimize electromagnetic interference (EMI) and crosstalk, leading to improved signal integrity.
Easier Maintenance: When repairs or replacements are necessary, wire harnesses simplify the process since the connections are well organized and labeled.
Cost-Effectiveness: While the initial setup and design of wire harnesses may require investment, in the long run, they can lead to cost savings due to reduced labor time, improved reliability, and easier maintenance.
Applications
Automotive: Wire harnesses are extensively used in the automotive industry to connect various electrical and electronic components in vehicles, such as engine and transmission systems, infotainment systems, lights, sensors and more.
Defense & Security: In aircraft and aerospace applications, wire harnesses play a crucial role in connecting avionic systems, navigation systems, communications systems, and various other electrical equipment.
Communications: Wire harnesses are employed in consumer electronics, industrial machinery, and computer systems to establish connections between different components and to ensure efficient signal transmission.
Medical: Wire harnesses are used to interconnect different sensors, monitors, and devices with medical devices and diagnostic equipment.
Industrial: Wire harnesses are used in industrial automation and machinery to establish connections between control panels, motors, sensors, and other components.
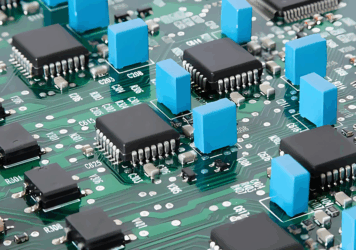
Mastering Thermal Management in PCB and Flex Circuit Design
As electronic devices become more compact and powerful, managing heat effectively is critical to ensuring performance, reliability, and long product...
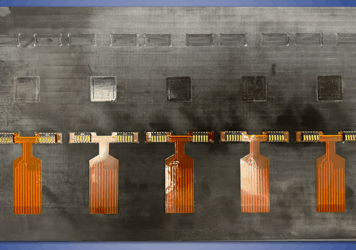
Step-by-Step Guide to the Flex Printed Circuit Board Assembly (FPCBA) Process
IntroductionAs electronics evolve to become thinner, lighter, and more complex, Flex Printed Circuit Boards (FPCBs) have emerged...
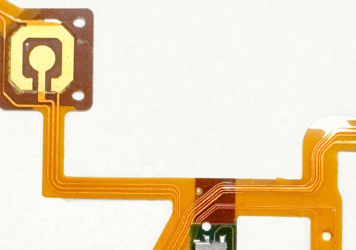
Designing for Precision: Controlled Impedance in Flexible Circuits
As electronic devices shrink and signal speeds increase, one design requirement becomes mission-critical: controlled impedance. This is...
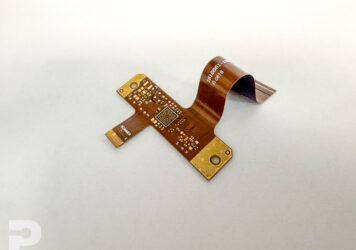
Bending Without Breaking: How Flexible Circuits Are Tested for Reliability
Flexible circuits are built to bend—but only when designed and tested to handle real-world mechanical demands. Whether...

Embedding Performance: How Passive Components Are Integrated into Flexible Circuits
As electronic devices evolve to become smaller, smarter, and more power-efficient, engineers are under increasing pressure to maximize performance within...
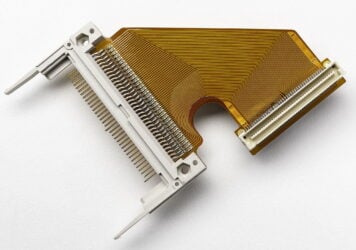
Designing for HDI PCB and Fine-Line Etching: What You Need to Know
As devices shrink and performance demands grow, engineers are turning to High-Density Interconnect (HDI) technology to pack...
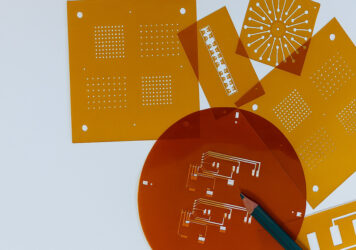
Kapton Etching in Flex Circuit Manufacturing: Processes, Materials, and Considerations
In the world of flexible electronics, polyimide films like Kapton® (a DuPont trademark) are a foundational material. Used in everything...
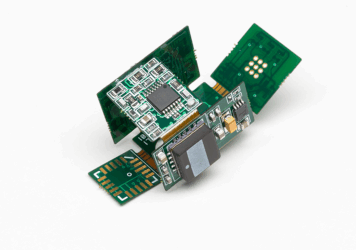
Designing Rigid-Flex Circuits: What Engineers Need to Know
Rigid-flex PCBs combine the best of both worlds—the durability of rigid boards and the versatility of flexible circuits—into a...
Request Your PICAKit Today
We want you to take a look at what we can produce for you by offering you a PICAKit which includes a variety of flexible pcb, shields, & flat flexible cables.
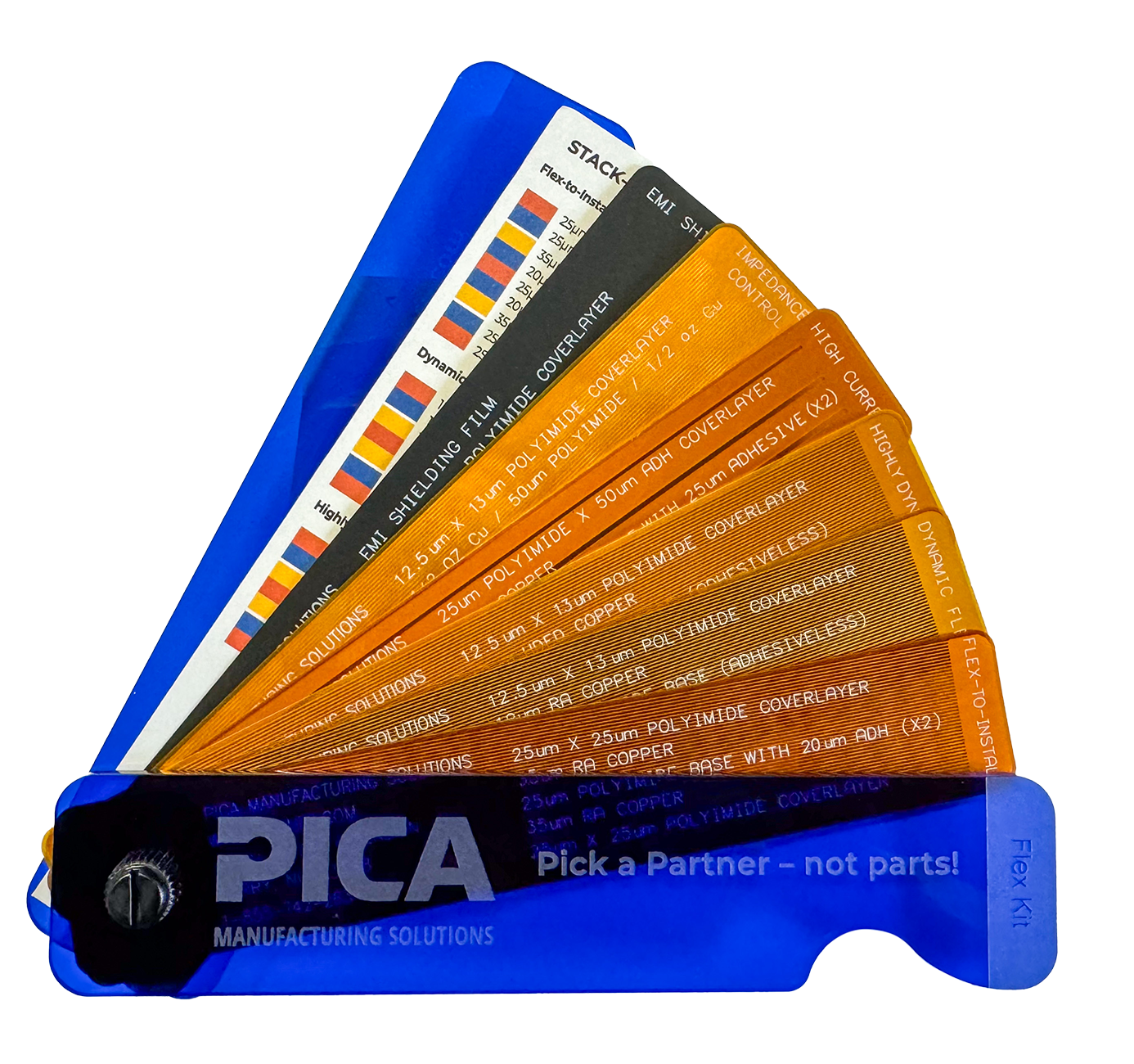